Cavitation Tunnel
Laboratory Manager : Dr.-Ing. Jens Neugebauer Cavitation Tunnel K23
Ideally, cavitation tunnel tests are the basis of an efficient ship design. The transmission of powers by the propeller is combined with an unwanted physical occurrence, so-called cavitation.
On both sides of the individual propeller wings the pressure can drop so much that it falls below the steam pressure of the water. The water begins to vaporise at room temperature and pressure and side cavitation occurs. Particularly, collapsing steam bubbles cause erosion to propeller and rudder which should be avoided by all means. By cavitation tunnel tests, the general danger of cavitation as well as the areas where it frequently occurs can be investigated.
The characteristic of the propeller in homogeneous currents, the so-called open-water propeller test, can also be determined in the cavitation tank. Thrust and torque are measured and the propeller efficiency is calculated. These data are collected in a typical open-water diagram.
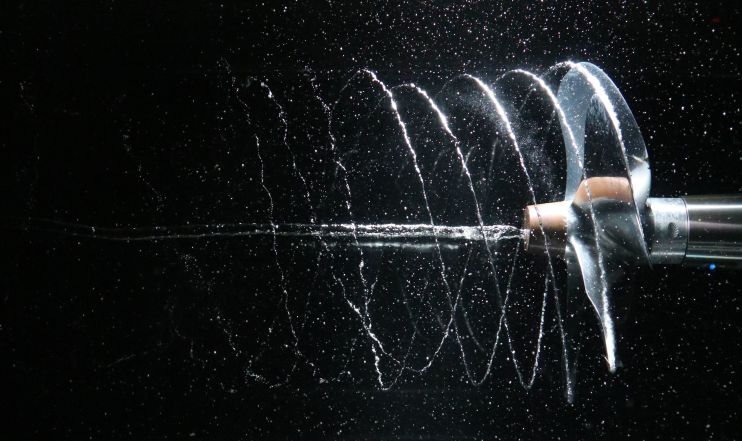
Cavitation tank K23 - Kempf & Remmers (Year of manufacture: 1963)
Measuring section: | 1100 mm x 300 mm x 300 mm |
Fluid velocity: | 9m/s max. |
Propeller diametre: | 15 cm max. |
Pressure: |
0,1 - 2 bar |
The dynamometer reaches a maximum of 5000min-1 and can transmit and measure forces of up to 500N and torques of up to 10Nm. The measurements are carried out via strain gauges for forces, differential pressure sensors for current velocity and pulse counters for rotational frequency. The sensor technology has been thoroughly revised and renewed recently and the measuring signals are acquired and processed with a measuring amplifier. Additionally, local velocities as well as velocity fields can be recorded with a laser-doppler anemometer, by means of a 2D linear motion system (e.g. the propeller wake).
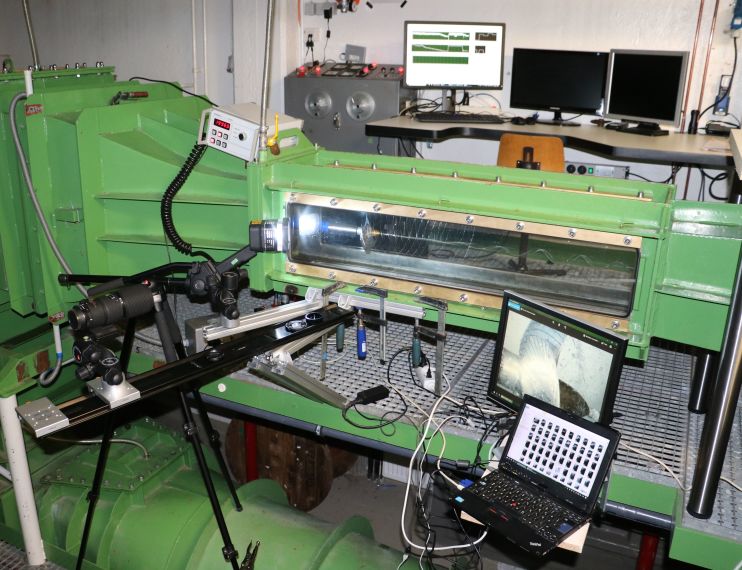